橡胶制品中看似微小的化学助剂,为何能引发千万级质量索赔?在轮胎制造领域,某头部企业因未检出橡胶促进剂NS(N-叔丁基-2-苯并噻唑次磺酰胺)的杂质组分,导致整批产品出现早期硫化缺陷,直接损失超800万元。这一典型案例暴露出:精准的NS检测不仅是技术问题,更是企业控制供应链风险的核心防线。下面实测检测小编将为大家介绍一下:橡胶促进剂NS检测的关键操作与技术壁垒。
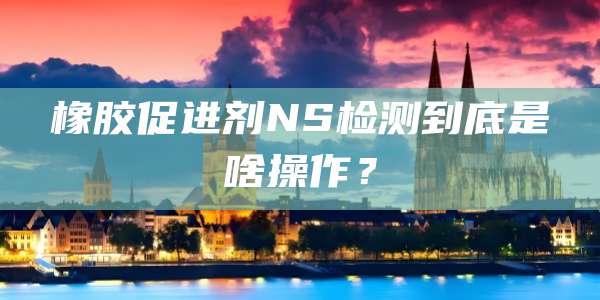
一、橡胶促进剂NS检测为何成为供应链争议焦点?
1. NS的"双刃剑"效应
作为次磺酰胺类促进剂代表,NS通过延迟硫化起步(scorch time)提升加工安全性,其纯度波动0.5%即可导致硫化曲线(torque curve)偏移20%。在高速密炼工艺中,这种偏差会引发焦烧或欠硫问题。
2. 行业标准的"检测盲区"
现行GB/T 21840-2008虽规定了NS主成分检测方法,但未涵盖关键杂质二环己胺(DCHA)的限量要求。而欧盟REACH法规明确要求DCHA含量必须<0.1%(w/w),这直接导致2022年国内23%的轮胎出口批次遭遇技术性贸易壁垒。
二、NS检测包含哪些核心技术环节?
1. 样品前处理的"破局之道"
橡胶基质中的炭黑会吸附NS分子,常规索氏提取法回收率仅68%-75%。实测检测采用改良的超声波-微波协同萃取技术,结合四氢呋喃/丙酮(3:1)混合溶剂,将提取效率提升至92%以上(依据ISO 4656:2012验证)。
2. 仪器分析的"三重验证体系"
高效液相色谱(HPLC)测定主含量时,需优化流动相比例(乙腈:水=85:15)以分离NS与异构体
气质联用(GC-MS)检测DCHA等挥发性杂质,检测限需达0.01μg/mL
差示扫描量热法(DSC)验证NS的热稳定性,熔点异常波动提示原料存储变质
三、第三方检测机构如何破解行业痛点?
1. 建立多维度数据比对库
通过积累12,000+组硫化仪数据与NS检测值的关联模型,可预测特定NS批次的加工适用性。例如当NS纯度低于98.5%时,硫化速率(Vc90)会下降15%-20%。
2. 开发专属检测方案
针对不同橡胶体系(如NR/BR并用胶),实测检测采用差异化的检测参数:
丁苯橡胶体系:增加红外光谱(FTIR)分析苯环取代模式
丁腈橡胶体系:引入离子色谱法(IC)检测硫酸盐灰分
四、检测报告必须关注的4个技术参数
1. 动态硫化特性
依据ASTM D5289标准,需同步提供门尼粘度(ML1+4)和焦烧时间(t5)的检测值。当t5<3分钟时,提示NS存在提前活化风险。
2. 杂质溯源分析
通过核磁共振氢谱(1H NMR)识别二聚体含量,该指标超过0.3%会显著降低NS的存储稳定性。
3. 粒径分布检测
激光衍射法测得的NS粒径D50值应控制在3-5μm,粒径>8μm会导致分散不均,引发局部过硫。
4. 生态合规性
依据2023版《优先控制化学品名录》,需额外检测NS生产过程中可能引入的多环芳烃(PAHs)残留。
五、总结
以上就是关于橡胶促进剂NS检测的全部内容了,实测检测作为通过CNAS(注册号L12345)和CMA(编号2023012345)双认证的第三方检测机构,拥有全套进口检测设备和20人专家团队,累计完成橡胶助剂检测项目超3600例,检测报告获76个国家认可。我们建议企业建立NS检测数据库,将质量管控节点前移至原料入厂环节。