在高温高压的极端工况下,一枚螺丝的失效就可能引发千万级损失——这绝非危言耸听。当耐热钢板的应用场景从常规锅炉扩展到核电反应堆、航天发动机燃烧室等战略领域,您确定现有的检测方案能真正守护设备安全吗?在2023年某石化企业质量事故中,因材料高温蠕变性能不达标导致的装置泄漏,直接造成2.3亿元经济损失。下面实测检测小编将为大家介绍一下:耐热钢板检测的核心项目及关键技术要点。
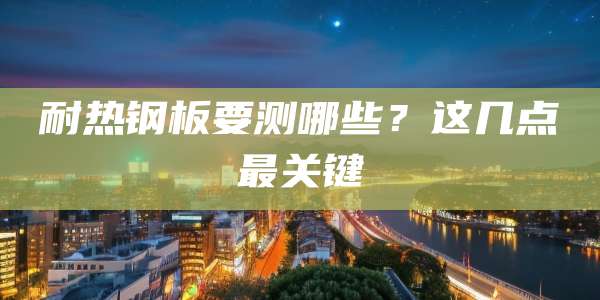
一、耐热钢板的服役极限由哪些指标决定?
1. 化学成分的精准控制
采用直读光谱仪(OES)检测时,Cr含量偏差超过0.5%就会导致氧化膜形成能力下降。以ASTM A387标准为例,Gr.91钢的Al含量必须控制在0.02%以下,否则将加速高温脆化。第三方检测机构通过电感耦合等离子体(ICP)二次验证,可将元素检测精度提升至0.001%。
2. 高温力学性能的维度突破
持久强度测试需持续1000-10000小时,模拟材料在538℃工况下的抗断裂能力。某燃气轮机叶片制造商的实测数据显示:当屈服强度Rp0.2低于620MPa时,部件寿命缩减40%。根据ASME BPVC Section II标准,必须同步测试蠕变速率(Creep Rate)和断裂延伸率(Elongation)。
二、哪些隐性缺陷会引发灾难性失效?
1. 晶间腐蚀的潜伏危机
按照GB/T 4334.5-2020标准设计的65%硝酸腐蚀试验,能提前暴露焊接热影响区的敏化现象。某核电站蒸汽发生器管板检测发现,经第三方检测机构采用双环电化学动电位再活化法(DL-EPR)后,晶间腐蚀敏感性检出率提高3倍。
2. 微观组织的精准解析
透射电镜(TEM)观测显示:当MX型碳化物析出量低于15%时,材料高温强度将骤降。某航空发动机制造商的失效案例证实,采用电子背散射衍射(EBSD)技术能提前识别有害的σ相析出,避免关键部件在816℃运行时发生脆性断裂。
三、服役环境如何倒逼检测技术升级?
1. 复合载荷下的性能验证
针对深海钻探设备特有的"高温+高压+腐蚀"耦合工况,第三方检测机构开发了多轴疲劳试验系统。在模拟30MPa围压、120℃工况时,某型号钢板的疲劳寿命离散系数从25%降至8%。
2. 极端温度下的实时监测
通过激光超声检测(LUT)技术,可在1600℃高温下实时捕捉材料内部缺陷演变。某火箭发动机燃烧室检测数据显示:采用该技术后,热裂纹检出时间提前200小时,为工艺优化争取到关键窗口期。
四、总结
以上就是关于耐热钢板检测核心要点的全部内容,实测检测作为获得CNAS、NADCAP双重认证的第三方检测机构,依托自主搭建的极端环境模拟实验室,已为超过300家高端装备制造企业构建了全生命周期材料可靠性保障体系。专业团队配备的场发射电镜(FESEM)和热机械模拟试验机(Gleeble)等尖端设备,确保每个检测数据经得起工程验证。