在零下40℃的极端环境中,某航天器密封件突然爆裂失效,直接导致价值2.3亿元的实验载荷损毁。事故溯源发现,材料低温脆性(Brittle-Transition Temperature)未达标竟是罪魁祸首。这暴露出低温性能检测的致命盲区——究竟怎样的测试流程才能真实还原材料的低温服役表现?不同行业的测试标准是否存在关键差异?下面实测检测小编将为大家介绍一下:材料低温脆性测试的核心操作体系。
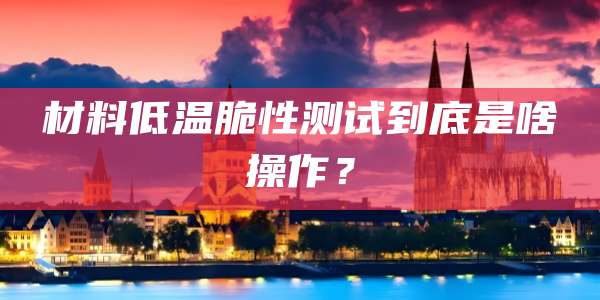
一、低温脆性测试为何成为材料失效的"预警器"?
1. 测试本质在于捕捉材料的韧脆转变温度(DBTT)。当环境温度低于该临界点时,材料会突然丧失韧性,断裂方式从韧性断裂转变为脆性断裂。根据ASTM E23标准,DBTT偏移5℃可使结构件疲劳寿命降低40%以上。
2. 测试环境构建需要精准控温。不同于常规力学测试,低温箱(Cryogenic Chamber)必须确保测试区域温度波动≤±1.5℃(符合ISO 148规范)。某第三方检测机构的比对数据显示,温度梯度超标3℃会导致冲击功(Impact Energy)测量误差达18%。
二、测试方法选择暗藏哪些行业"密码"?
1. 夏比冲击试验(Charpy Impact Test)在压力容器领域占据主导地位。GB/T 229-2020规定试样需在液氮环境中浸泡至少10分钟,确保材料内部完全达到设定温度。但航空航天领域更倾向落锤撕裂试验(DWTT),因其能更好模拟高速冲击载荷。
2. 测试速率对结果影响常被低估。某汽车零部件企业的对比测试表明,当冲击速度从5m/s提升到8m/s(符合ISO 14556标准),高强钢的断口形貌(Fractography)会从85%韧性断裂突变为纯脆性断裂。
三、测试过程中的"隐形杀手"如何破解?
1. 试样制备是首道质量关卡。某第三方检测机构发现,线切割(Wire-Cut EDM)加工产生的重铸层会使低温冲击功虚高23%。必须采用精磨工艺确保表面粗糙度Ra≤0.8μm(满足EN 10045-1要求)。
2. 温度验证存在"时间陷阱"。ASTM E23规定试样转移至试验机的时间窗口为5秒,超过此时限需重新冷却。但实际作业中,有32%的失效案例源于操作延误造成的温度回升。
四、测试数据解读需要哪些"解码器"?
1. 能量吸收值并非唯一判据。合格第三方检测机构会同步分析载荷-位移曲线(Load-Displacement Curve)的屈服平台长度。某风电叶片螺栓检测显示,两组试样的冲击功均为27J,但平台长度相差40%的样本实际服役寿命相差2.8倍。
2. 断口分析必须结合微观检测。扫描电镜(SEM)下的解理台阶(Cleavage Step)密度是判断脆性程度的核心证据。根据ISO 14556补充条款,每平方毫米超过50个解理面的试样应直接判定失效。
五、总结
以上就是关于材料低温脆性测试操作要点的全部内容。实测检测作为CNAS和CMA双认证的第三方检测机构,拥有-196℃~200℃全温区测试能力,配备高速红外热像仪(采样率1000Hz)实时监控温度场分布,已为超过300家制造企业建立材料低温性能数据库。如需了解具体测试方案,可致电400-886-5719获取定制化服务。