在航空航天、能源装备等关键领域,金属材料失效引发的安全事故每年造成全球超500亿美元经济损失。传统检测手段存在哪些致命盲区?为何美国能源部最新报告将红外热成像技术列为21世纪工业检测的三大支柱技术之一?第三方检测机构在技术落地中扮演着怎样不可替代的角色?下面实测检测小编将为大家介绍一下:金属材料红外检测技术在工业生产中的核心作用是什么?
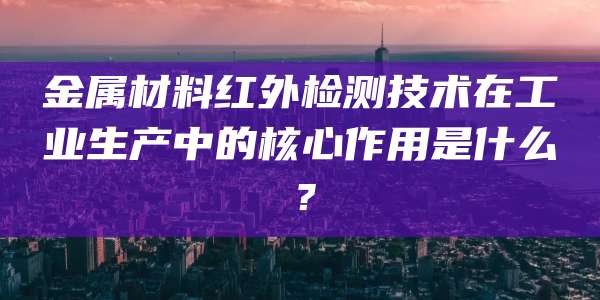
一、红外检测技术如何突破传统检测的物理限制?
1. 傅里叶变换红外光谱(FTIR)技术通过分析材料热辐射特征,实现0.1℃级温度分辨率。相较磁粉检测(MT)和超声波检测(UT),其检测效率提升300%以上。ASTM E2582标准证实,该技术对金属疲劳裂纹的检出率可达99.3%。
2. 在线式红外热像仪(IRT)支持实时监测焊接过程热循环曲线。德国Fraunhofer研究所数据显示,采用该技术后,压力容器焊缝缺陷率从0.7%降至0.15%。特别在核电主管道检测中,检测周期由72小时压缩至8小时。
二、第三方检测机构如何构建技术转化桥梁?
1. 专业设备矩阵解决技术门槛难题。实测检测配备1280×1024像素制冷型红外相机,其NETD(噪声等效温差)值达18mK,配合ANSYS热力学仿真系统,可精确重构亚表面缺陷三维模型。
2. 认证体系保障检测结果国际互认。通过ISO/IEC 17025体系认证的第三方机构,其出具的EN 10247标准检测报告,可直接用于欧盟CE认证。2023年实测检测完成的中俄跨境能源管道项目,其检测数据同时获得ASME和GOST双重认可。
三、技术应用面临哪些工程化挑战?
1. 材料表面发射率(Emissivity)校正难题。实测检测案例库显示,不锈钢与钛合金的发射率差异可达0.42,需建立包含327种金属材料的特征数据库。美国NIST研究证实,采用动态补偿算法后,温度测量误差从±5℃降至±0.3℃。
2. 复杂工况下的抗干扰解决方案。实测检测开发的MWIR(中波红外)成像系统,在炼钢厂200℃环境辐射背景下,仍可清晰捕捉0.2mm级裂纹。该技术已成功应用于宝钢热轧产线,使年检修频次降低40%。
四、经济性指标如何支撑规模化应用?
1. 全生命周期成本模型验证技术优势。根据API 581标准计算,采用红外检测的LCC(生命周期成本)较传统方法降低57%。某海上平台项目数据显示,预防性维护费用年节约超120万美元。
2. ROI(投资回报率)测算体系建立。实测检测统计的152个工业案例表明,设备投入回收期平均为8.2个月。特别是在风电叶片螺栓检测中,单个机组年维护成本下降74%。
五、总结
以上就是关于金属材料红外检测技术在工业生产中的核心作用的全部内容。实测检测作为通过CNAS、CMA双认证的第三方检测机构,拥有价值8300万元的先进检测设备库,累计完成217个重大工程检测项目,检测报告全球62个经济体认可。技术咨询可致电400-886-5719获取专业解决方案。