在工业制造领域,铝材因其轻量化、高强度和耐腐蚀性成为关键材料,但您是否了解:若材质性能不达标,可能导致结构件断裂、设备故障甚至安全事故?据行业统计,2024年因材料缺陷引发的工程事故中,铝材占比高达27%。如何通过科学检测确保铝材性能符合严苛的工程需求?哪些基础测试项目是质量控制的“必选项”?下面实测检测小编将为您解析铝材材质检测的核心性能测试体系。
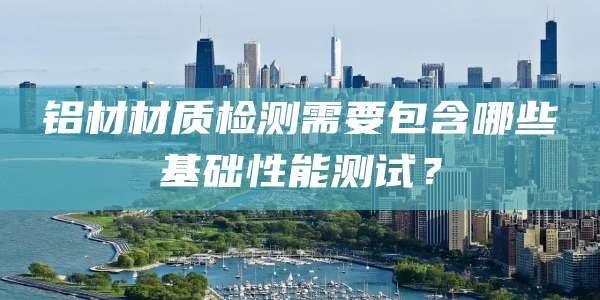
一、化学成分分析为何是铝材检测的基石?
1.元素含量精准控制
铝材的力学性能和耐蚀性直接受合金元素(如Si、Mg、Cu)含量影响。以6061-T6铝合金为例,GB/T 3190-2008规定镁含量需控制在0.8%-1.2%,硅含量为0.4%-0.8%。第三方检测机构通过光谱分析(OES)和电感耦合等离子体发射光谱(ICP-OES)技术,可精确测定12种主量及微量元素,偏差精度达±0.01%。
2.杂质限值判定
铁(Fe)元素超标会显著降低铝材延展性。例如,建筑型材中Fe含量超过0.35%即判定为不合格(依据GB/T 5237.1-2017)。通过化学滴定法与X射线荧光光谱(XRF)联用,可同步检测重金属及有害物质(如Pb、Cd),满足RoHS和REACH法规要求。
二、机械性能测试如何保障材料承载能力?
1.强度与塑性的平衡
拉伸试验(GB/T 228.1-2021)可测定抗拉强度(Rm)、屈服强度(Rp0.2)和断后伸长率(A)。例如,航空用7075-T6铝合金要求Rm≥540 MPa、A≥10%。第三方检测机构采用微机控制电子万能试验机,加载速率精度达0.5%/s,确保数据符合ISO 6892-1国际标准。
2.动态载荷适应性
夏比冲击试验(GB/T 229-2020)模拟材料在低温或高速冲击下的韧性。数据显示,冲击功低于27 J的铝材在-20℃环境中脆断风险增加83%。通过液氮温控系统,可实现-196℃至300℃全温域测试。
三、物理性能参数对应用场景有何指导意义?
1.热力学特性验证
热膨胀系数(CTE)检测可预判材料在温差环境中的形变量。例如,高铁车厢用5083铝合金CTE需控制在23.8×10^-6/℃(GB/T 4338-2016),偏差超5%将导致焊接接头开裂。
2.导电与导热优化
电导率测试(涡流法)可评估铝材在电力传输中的损耗。国际电工委员会(IEC)规定,架空导线用1350铝合金电导率不得低于61% IACS,第三方检测机构采用四探针法检测,误差小于0.5%。
四、表面质量缺陷如何影响材料服役寿命?
1.微观缺陷定位
金相分析(GB/T 3246.1-2012)通过扫描电镜(SEM)观察晶粒度(目标值5-7级)和相分布。数据显示,晶粒粗化(>8级)会使疲劳强度下降40%。
2.氧化膜完整性
阳极氧化膜厚度检测(涡流法)是防腐关键指标。建筑型材膜厚需≥10 μm(GB/T 5237.2-2017),第三方检测机构通过横截面显微测量法,分辨率达0.1 μm。
五、耐腐蚀性测试为何是环境适应性的核心指标?
1.加速老化模拟
中性盐雾试验(GB/T 10125-2021)可评估材料在海洋气候中的耐蚀等级。例如,汽车用6005A铝合金需通过3000小时盐雾测试,腐蚀速率<0.05 mm/年。
2.应力腐蚀敏感性
通过慢应变速率试验(SSRT)测定应力腐蚀开裂阈值(KISCC)。航空用2024-T3铝合金要求KISCC≥22 MPa·m^0.5,第三方检测机构采用恒载荷法,精度达±1.5%。
六、总结
以上就是关于铝材材质检测基础性能测试的全面解析。实测检测作为专业第三方检测机构,拥有CMA和CNAS双重资质,配备光谱仪、电子万能试验机等尖端设备,可为企业提供从成分分析到环境适应性测试的一站式解决方案,确保铝材性能100%符合国标、ISO及ASTM要求。