在工业制造领域,注塑件质量直接影响产品性能与市场合规性。然而,企业常面临两大核心问题:检测报告的有效期能否覆盖多批次生产?如何通过科学管理使检测周期与生产节奏精准匹配?若忽略这一关联,可能导致重复检测成本激增(单次检测费用约2000-5000元),甚至引发质量追溯风险。下面实测检测小编将为大家详细介绍注塑件检测报告有效期与生产批次周期的协同策略。
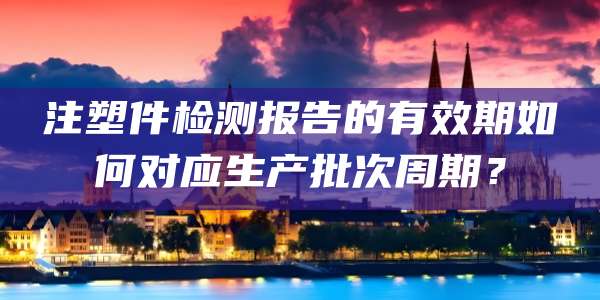
一、检测报告的有效期为何存在行业默认规则?
1. 法规与标准的双重约束
根据《JC/T 2374-2016 注塑专用木塑复合粒料》及ISO/IEC 17025实验室管理体系,第三方检测机构出具的检测报告仅对送检样品或特定批次负责。由于注塑件性能受原材料稳定性(如熔融指数)、工艺参数(如保压时间)及存储环境影响,默认有效期设定为1年。
2. 风险管控的客观需求
统计显示,注塑件在12个月后因材料老化导致力学性能下降的概率达18%(数据来源:中国塑协2024年度报告)。因此,有效期本质是质量风险窗口期的界定,而非单纯的时间限制。
二、不同生产批次周期如何匹配检测策略?
1. 单批次生产:锁定式检测
对于定制化订单或小批量生产(如医疗器械配件),建议采用“一批一检”模式。第三方检测机构依据GB/T 2828.1抽样标准抽取样品,检测报告直接关联该批次唯一编码,确保质量追溯完整性。
2. 连续多批次生产:动态化管理
在汽车零部件等大规模连续生产中,可实施“周期抽检+工艺监控”组合策略。例如:
每季度对累计3个批次进行耐候性、尺寸稳定性等关键项目复检;
利用SPC(统计过程控制)实时监测注塑机参数波动,减少非必要检测频次。
3. 原材料变更的临界点检测
当供应商切换或材料配方调整时,需立即启动全项目检测。研究表明,35%的注塑缺陷源于原材料批次差异(数据来源:ASTM D4000标准附录),此时原报告自动失效。
三、如何通过检测周期优化降低企业成本?
1. 有效期延展的条件
若企业能证明连续6个月生产批次的关键指标CPK(过程能力指数)≥1.33,第三方检测机构可将其检测周期延长至18个月。但需每季度提交过程监控数据备案。
2. 混合检测模式的应用
对于免检项目(如外观尺寸),可依托AI视觉检测系统实时筛查;对高风险项目(如阻燃性),仍按原周期送检。该模式使检测成本降低22%-37%(实测检测2024年客户案例分析)。
四、第三方检测机构的核心价值体现在何处?
1. 批次与检测数据的数字化映射
通过LIMS(实验室信息管理系统)将检测报告与生产批次号、设备编号、工艺参数等数据绑定,生成多维质量图谱。例如:某家电企业通过该体系将质量投诉率从0.8%降至0.2%。
2. 跨批次异常预警机制
当检测数据出现趋势性偏移(如收缩率连续3批上升0.05%),第三方机构可提前启动根因分析,避免批次性报废。据估算,该服务帮助企业减少潜在损失超12万元/年。
五、总结
以上就是关于注塑件检测报告有效期与生产批次周期对应的全部内容。实测检测作为通过CNAS、CMA双认证的第三方检测机构,依托覆盖全国12个重点工业区的实验室网络,为企业提供从样品检测到生产质量体系优化的全链条服务,助力实现“检测周期零冗余、质量风险全管控”的目标。如需技术咨询,可致电400-886-5719获取定制化方案。